Case Study: Contract Testing Laboratories with Multiple Locations
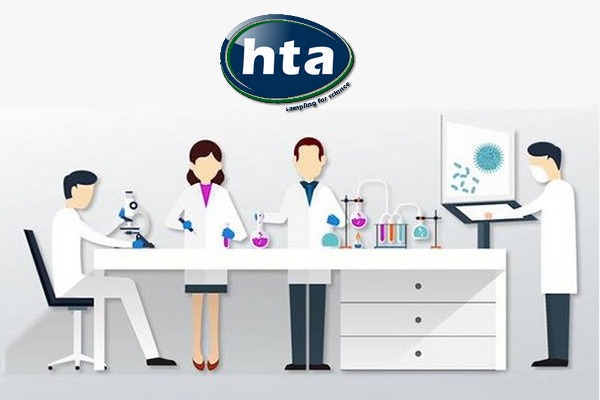
Background
Contract testing laboratories with multiple locations face unique challenges in managing and reallocating equipment across diverse sites. In these large organizations, priorities shift constantly to meet client needs, and assets are frequently moved to adapt to dynamic workloads and organizational changes.
Challenge #1: Asset Reallocation Due to Workload Variations
Workload demands in contract testing laboratories can fluctuate significantly based on client requirements, seasonal projects, or new contracts. As testing activities are reassigned across labs, labs may need to transfer assets—including analyzers and autosamplers—to balance workloads across sites. This movement ensures that high-demand labs have the necessary equipment on-site, maximizing operational efficiency and reducing project backlogs. However, with traditional analyzer-specific peripherals, each move requires significant time, cost, and effort to reconfigure new, compatible autosamplers at every location.
Challenge #2: Mergers and Acquisitions Leading to Asset Redistribution
Large contract testing organizations frequently undergo mergers and acquisitions (M&A) as they expand service offerings or integrate complementary expertise. When this happens, the newly combined entity must redistribute assets to ensure that each location has the appropriate equipment for its specialized activities. Often, this involves moving analyzers and autosamplers from one lab to another, sometimes across states or countries. Without compatible, cross-platform autosamplers, M&As can lead to increased spending on new peripherals, setup delays, and operational inefficiencies as labs reconfigure their equipment.
Challenge
Reallocating analyzers between lab sites presents several issues for contract testing labs:
- Incompatible Peripherals: Analyzers often come equipped with autosamplers designed for specific testing scopes, which may not align with requirements at a new site.
- Redundant Equipment Costs: When analyzers are reallocated, new autosamplers may be required, increasing equipment costs and creating redundant assets.
- Operational Downtime: Setting up new systems and retraining staff on different peripherals can interrupt workflow, impacting service continuity and productivity.
Solution
The solution is choosing HTA’s independent autosamplers for flexible asset reallocation and cost efficiency.
HTA offers independent, all-in-one autosamplers that integrate seamlessly with various chromatographs and spectrometers. This flexibility allows contract testing labs to reallocate analyzers across different locations without the need to purchase new peripherals, minimizing costs and maximizing asset utility.
Implementation
A large contract testing laboratory network recently faced a project shift that required moving analyzers across multiple lab sites. By equipping these analyzers with HTA’s all-in-one autosamplers, they ensured seamless compatibility across their various testing environments.
In one instance, an analyzer was moved from a quality control lab to a site specializing in environmental testing. Thanks to the HTA autosampler’s flexibility, it was immediately operational upon arrival, meeting the new lab’s requirements without the need for new peripherals.
Implementation Process:
- Compatibility Assessment: HTA’s team verified that the autosamplers could work across all sites and analyzer models used by the organization, ensuring compatibility with each location’s unique testing needs.
- Effortless Reallocation: The HTA autosamplers were transferred with analyzers to new sites without additional setup requirements, avoiding delays and reducing equipment costs.
- Uninterrupted Workflow: HTA’s user-friendly autosamplers required no significant retraining, allowing staff at the new location to integrate them immediately into operations.
Results
Within six months of integrating HTA’s autosamplers, the laboratory network achieved the following benefits:
- Reduced Equipment and Training Costs: By reusing HTA autosamplers across locations, the network saved significantly on new peripheral purchases and avoided retraining costs.
- Improved Operational Flexibility: HTA’s adaptable autosamplers enabled smooth analyzer reallocation across sites, allowing the organization to meet evolving client needs without compatibility concerns.
- Streamlined Operations: HTA’s autosamplers minimized downtime by allowing immediate integration at each site, ensuring uninterrupted productivity and rapid response to client demands.
Conclusion
HTA’s independent autosamplers empower contract testing laboratories with the flexibility to reallocate assets across multiple locations, reducing redundant costs and minimizing operational interruptions. By choosing HTA’s autosamplers, these laboratories can confidently meet changing client needs while maintaining budget efficiency and productivity. HTA’s solution allows labs to focus on delivering high-quality testing services, supporting a future-proof investment in laboratory infrastructure.
Contact usto learn how HTA’s autosamplers can optimize flexibility and cost-efficiency across your contract testing labs.
Latest News
- HOW TO VIDEO: Change mode in HTA All-in-one GC Autosampler
- HOW TO VIDEO: Add your HTA instrument to the Customer Portal
- Contact the HTA Sales Team on WhatsApp!
- The Importance of a Good Distributor in the Lab Industry
- HOW TO VIDEO: run calibration in your HTA Spectroscopy Autosampler
- HTA: New Spaces for a New Era
- Case Study: Contract Testing Laboratories with Multiple Locations
- Our New Headquarters: We Go Green
- Dear HTA, My Christmas wish is…
- Case Study: Future-Proofing Investments for Public Research Laboratories